TESTING THE FUTURE OF BATTERIES
Battery Testing
We specialize in providing comprehensive and cutting-edge battery testing services to meet the growing demands of the E-mobility and Energy Storage sectors. Our state-of-the-art facilities, expert team and renowned partners ensure that your batteries are rigorously tested for safety, performance, and reliability.
DRIVING INNOVATION
At the heart of the E-mobility revolution lies the battery, the crucial component driving innovation and performance. Understanding and validating new advancements are essential for the industrialization of next-generation battery technologies. That’s why together with our partners we offer comprehensive and rigorous testing services to ensure your innovations are ready for the future.
KEY TESTING AREAS
To ensure the highest standards of performance, safety, and abuse, we offer a broad spectrum of battery testing services tailored to meet the diverse needs of our clients. Our testing framework is divided into three main categories: Thermal, Electrical, and Mechanical, each designed to meticulously evaluate every aspect of battery functionality.
Analyze the batteries performance under normal working conditions
THERMAL
Thermal behavior
+ Validation of cell- and pack materials for heat conduction
+ Thermal analysis based on multi-point measurements and infrared
ELECTRICAL
Electrical behavior
+ Validation of inhouse prototype cells
+ Formation & Cycling
+ Impedance spectroscopy for the analysis of aging behavior
MECHANICAL
Mechanical behavior
+ Custom analyses mech. mounting
+ Effects of clamping/mounting on operation and lifetime.
+ Simulation-based analysis
Specific tests that address the safety-relevant parts of a battery, making batteries safer
Analysis of thermal propagation
+ Abuse testing of small battery modules
+ Implementing of different strategies to prevent propagation
+ Analysis of temperatures and heat flux
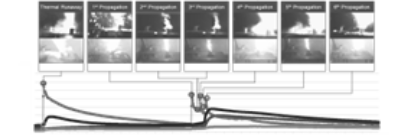
Fall-Safe mechanism
+ Evaluating the reliability of pressure vents and various additional materials between the cells
The battery is deliberately mishandled to evaluate its behavior under extreme conditions
Analysis of thermal runaway
+ Abuse testing of battery cells up to ~150 Ah
+ Abuse via heating, overcharge or penetration
+ Analysis of gas emission, particle composition and thermal process
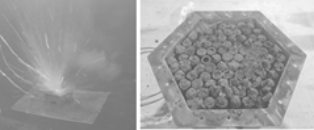
Injury tests
+ Mechanical analysis in terms of crush or penetration
+ Impact on safety and lifetime
+ CT-scans
Analyze the batteries regarding different properties
THERMAL
Thermal and Chemical Analytics
+ Thermal Shrinkage
+ SEM, EDX, ICP-OES, DSC/TGA, XRD
+ (Py-)GC-MS and XFR
+ NMR and ATR-FTIR Spectroscopy
ELECTRICAL
Electrical Analytics
+ Cyclisation
+ Electric circuit with sensor
MECHANICAL
Mechanical Analytics
+ Hg-Porosimetry
+ Confocal 3D microscopy
+ Tensile and Peeling test
PERFORMANCE
Analyze the batteries performance under normal working conditions
THERMAL
Thermal behavior
+ Validation of cell- and pack materials for heat conduction
+ Thermal analysis based on multi-point measurements and infrared
ELECTRICAL
Electrical behavior
+ Validation of inhouse prototype cells
+ Formation & Cycling
+ Impedance spectroscopy for the analysis of aging behavior
MECHANICAL
Mechanical behavior
+ Custom analyses mech. mounting
+ Effects of clamping/mounting on operation and lifetime.
+ Simulation-based analysis
SAFETY
Specific tests that address the safety-relevant parts of a battery, making batteries safer
Analysis of thermal propagation
+Abuse testing of small battery modules
+Impementing of different strategies to prevent propagation
+Analysis of temperatures and heat flux
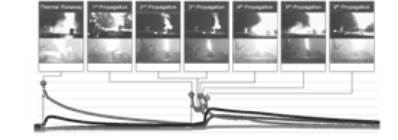
Fall-Safe mechanism
+ Evaluating the reliability of pressure vents and various additional materials between the cells
ABUSE
The battery is deliberately mishandled to evaluate its behavior under extreme conditions
Analysis of thermal runaway
+ Abuse testing of battery cells up to ~150 Ah
+ Abuse via heating, overcharge or penetration
+ Analysis of gas emission, particle composition and thermal process
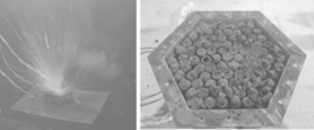
Injury tests
+ Mechanical analysis in terms of crush or penetration
+ Impact on safety and lifetime
+ CT-scans
ANALYTICS
Analyze the batteries regarding different properties
Thermal and Chemical Analytics
+ Thermal Shrinkage
+ SEM, EDX, ICP-OES, DSC/TGA, XRD
+ (Py-)GC-MS and XFR
+ NMR and ATR-FTIR Spectroscopy
Electrical Analytics
+ Cyclisation
+ Electric circuit with sensor
Mechanical Anaalytics
+ Hg-Porosimetry
+ Confocal 3D microscopy
+ Tensile and Peeling test
Advanced Testing Methods and Technologies
We leverage a diverse array of advanced testing methods and technologies to provide a thorough evaluation of battery components. These state-of-the-art testing methods allow us to thoroughly assess and validate battery technologies, ensuring they meet the highest standards for performance, safety, and longevity.
Electrode Testing Thermal Analysis
+SEM and EDX Analysis: Scanning Electron Microscopy with Energy Dispersive X-ray for detailed surface examination.
+ICP-OES Analysis: Inductively Coupled Plasma Optical Emission Spectroscopy for elemental analysis.
+DSC/TGA Analysis: Differential Scanning Calorimetry and Thermogravimetric Analysis for thermal properties.
+XRD Analysis: X-ray Diffraction for crystalline structure identification.
CHEMICAL ANALYSIS
+Scanning Electron (Py-)GC–MS: Pyrolysis Gas Chromatography-Mass Spectrometry for chemical composition.
+XRF: X-ray Fluorescence for material characterization.
+NMR Spectroscopy: Nuclear Magnetic Resonance for molecular structure analysis.
+ATR-FTIR Spectroscopy: Attenuated Total Reflectance Fourier Transform Infrared Spectroscopy for chemical bonding.
+Hg-Porosimetry: Mercury Porosimetry for porosity measurements.
+Thermal Shrinkage: Evaluation of material shrinkage under thermal conditions.
+Cyclisation: Testing of repeated charging and discharging cycles.
+Electric Circuit with Sensor: Monitoring electrical properties with integrated sensors.
+Thermal Propagation Tests: Analysis of thermal propagation within battery cells.
+Confocal 3D Microscopy: High-resolution 3D imaging for surface and internal structures.
ELECTRICAL MECHANICALAnalysis
+Tensile and Peeling Test: Measuring adhesion strength and mechanical durability.
+Drop Tower & Intrusion Body: Assessing impact resistance and structural integrity.
+Stress Test (Overload or High C Rates): Evaluating performance under high current rates.
+Impedance Spectroscopy: Analyzing impedance for battery health and aging.
+Dynamic Intrusion Test: Testing resistance to dynamic mechanical intrusion.
How We’re Revolutionizing Future
We offer a wide range of battery testing services, categorized into Standard and Special tests. Each category encompasses testing for battery material, battery cell, and battery system levels, ensuring a holistic evaluation of your battery technologies.
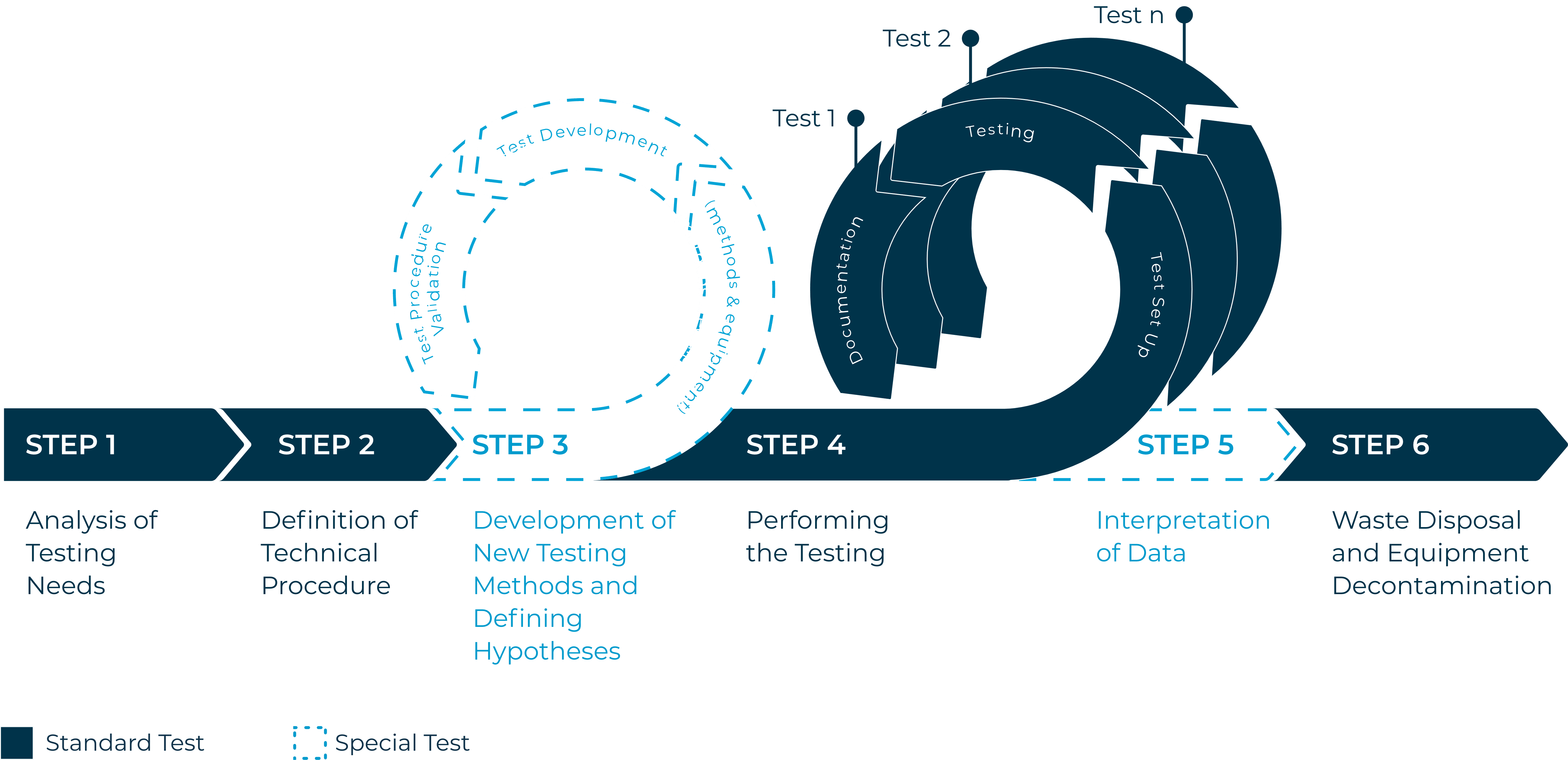
EXPLORE THE DETAILS
OF THE STEPS
STEP 1
Analysis of testing needs
The testing process begins with a comprehensive analysis of the client’s specific testing requirements. We work closely with our clients to understand the unique demands and objectives of their battery projects. This step involves evaluating the battery’s intended application, performance targets, and safety considerations. By thoroughly analyzing these needs, we ensure that our testing strategy is precisely tailored to meet the client’s goals, setting the stage for a successful validation process.
STEP 2
DEFINITION OF TECHNICAL PROCEDURES
We collaborate with the client and our partners to develop a detailed testing plan that outlines the specific methodologies and protocols to be used. This includes selecting the appropriate tests, determining the sequence of testing activities, and specifying the equipment and conditions required. By meticulously defining the technical procedure, we ensure that the testing process is systematic, reproducible, and aligned with the client’s objectives, leading to accurate and reliable results.
STEP 3
Development of New Testing Methods and Defining Hypotheses
Leveraging cutting-edge technology and unparalleled expertise, we develop customized testing methodologies to address your specific requirements. This crucial step involves a detailed discussion where we jointly outline the specific performance, safety, and reliability attributes the battery should exhibit. By establishing these expectations, we create a focused framework for our testing procedures, ensuring that every test is aligned with validating the predefined hypotheses and delivering insightful, actionable results.
STEP 4
PERFORMING THE TESTING
Through a series of rigorous evaluations, we analyze all aspects of your battery technology, from energy capacity to thermal stability. Our cutting-edge facilities and advanced testing equipment, provided by us or our partners, guarantee precise and dependable results, empowering you with the insights necessary for well-informed decisions. Whether you are developing new battery solutions or optimizing existing ones, our testing protocols give you the confidence you need to succeed in today’s competitive landscape.
STEP 5
INTERPRETATION OF DATA
Numbers alone don’t tell the whole story: that’s where our expertise in data interpretation comes in. Once the battery testing phase is complete, we drill down into the results to extract valuable information that allows us to make informed decisions. Our team of expert analysts meticulously examines the data, identifying patterns, trends, and anomalies that may affect performance or reliability.
STEP 6
Waste Disposal and Equipment Decontamination
In the final step of the testing process, we ensure careful and environmentally responsible disposal of hazardous materials generated during testing. Additionally, we thoroughly clean and decontaminate all equipment used in the testing process, preparing it for the next round of tests. By adhering to strict waste disposal protocols and maintaining a clean testing environment, we uphold the highest standards of laboratory safety and environmental stewardship.
WHY US?
By offering both Standard and Special testing services, PEM Motion ensures that your battery technologies are not only ready for today’s applications but also robust enough to meet the challenges of tomorrow.
EXPERTISE
+Over 10 Years of Experience
+Legal Assessment Support
KNOW-HOW
+Technical and Methodology Expertise
+Professional Battery Preparation
+Comprehensive Reporting
FULL PACKAGE
+One-Stop Full-Service Testing
+Data Security Assurance
INNOVATION
+Innovation Focus (Gen+3)
PARTNERS
+Collaborative Network
+>150m€ testing infrastructure in Aachen in our partner network
our partners
We believe in the power of partnerships to drive innovation and achieve excellence. We are proud to collaborate with a select network of partners who share our vision of leadership in the battery industry. These strategic partnerships enable us to deliver comprehensive, leading-edge solutions to our customers, while together driving technological progress and sustainability.
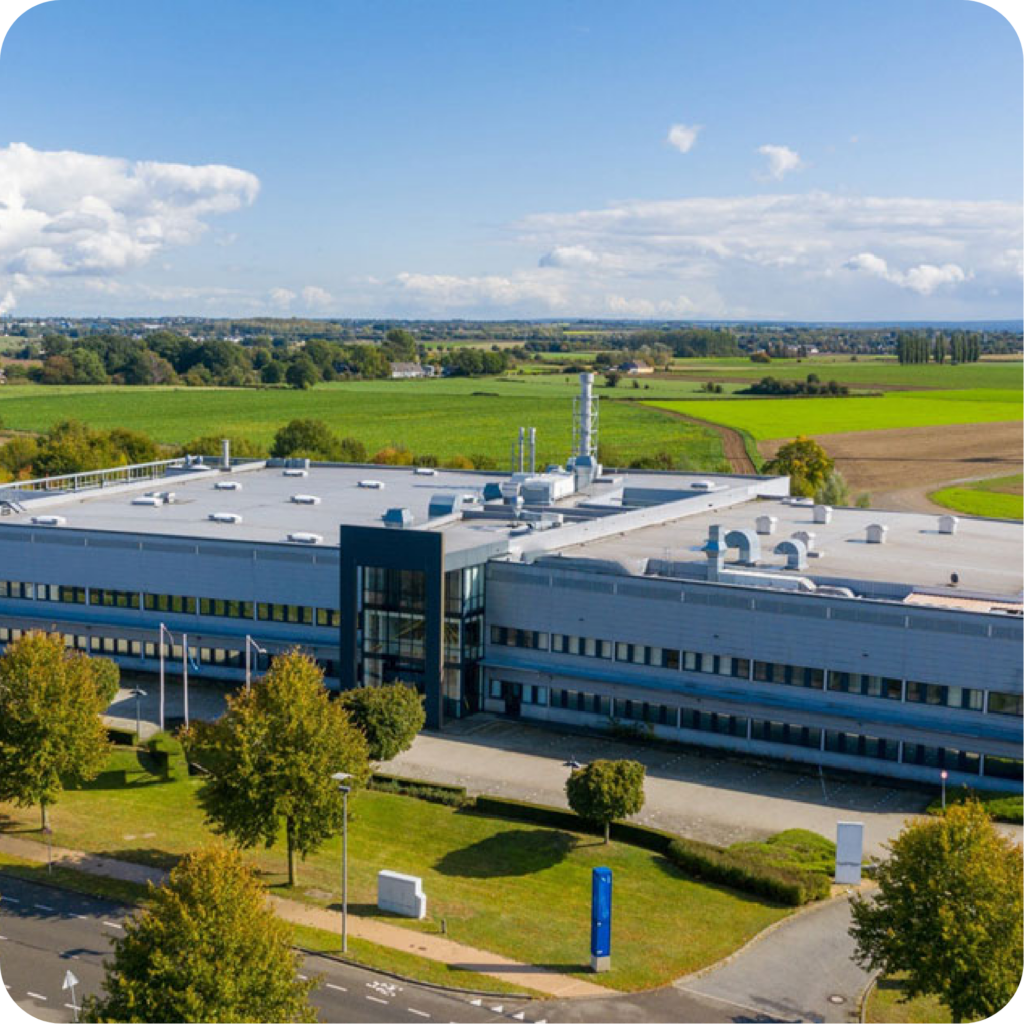
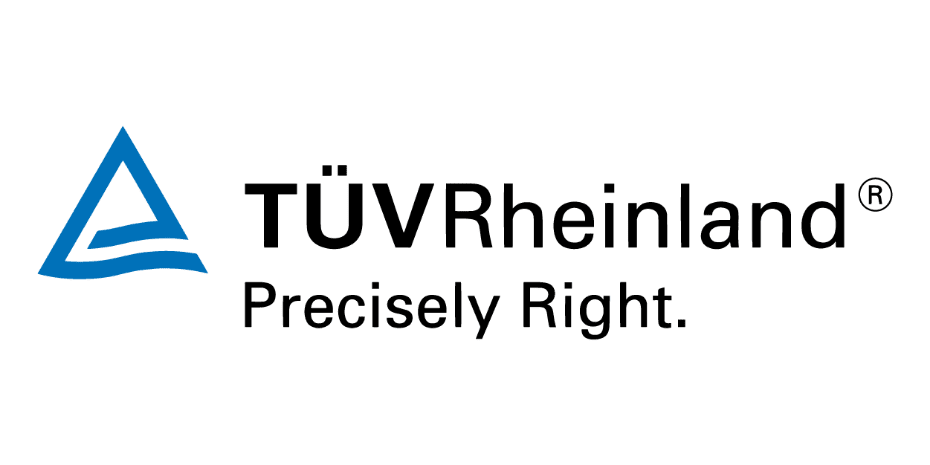
Offers precision testing services at its state-of-the-art complex. The facility is equipped with €24 million worth of cutting-edge technology spread across 2,200 square meters. Notably, its facilities boast battery testing capabilities of up to 800 kg with dimensions of 2.3 m x 1.6 m x 0.4 m (L x W x H), and an impressive 500 kW output (or 1,200 V; 1,000 A). The company adheres to the most stringent international testing standards, including ECE R100, UN 38.3, GB 38031, and LV124.
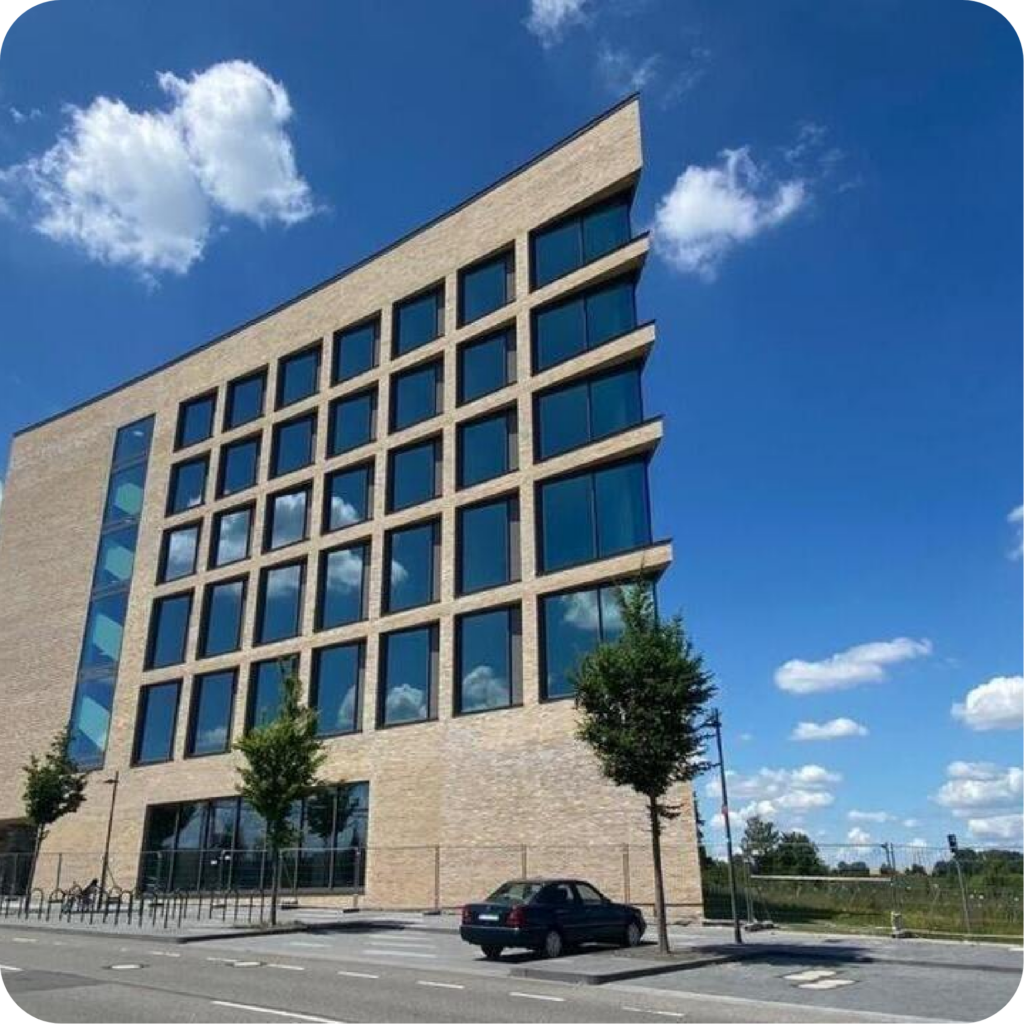
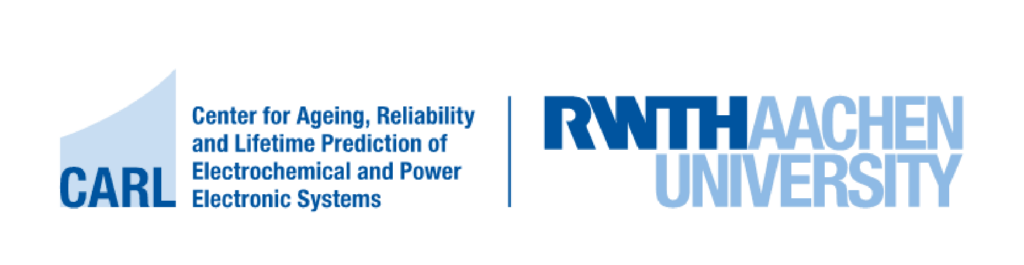
Offers an expansive battery research infrastructure spanning 5,000 square meters, backed by a €120 million investment. Their focus is on understanding the aging and lifetime of energy storage systems. They utilize cutting-edge technologies such as electron microscopes, computer tomographs, X-ray spectrometers, and mass spectrometers. The organization conducts environmental tests on battery cells, modules, and packs, supported by forty cell testers for continuous cycling.
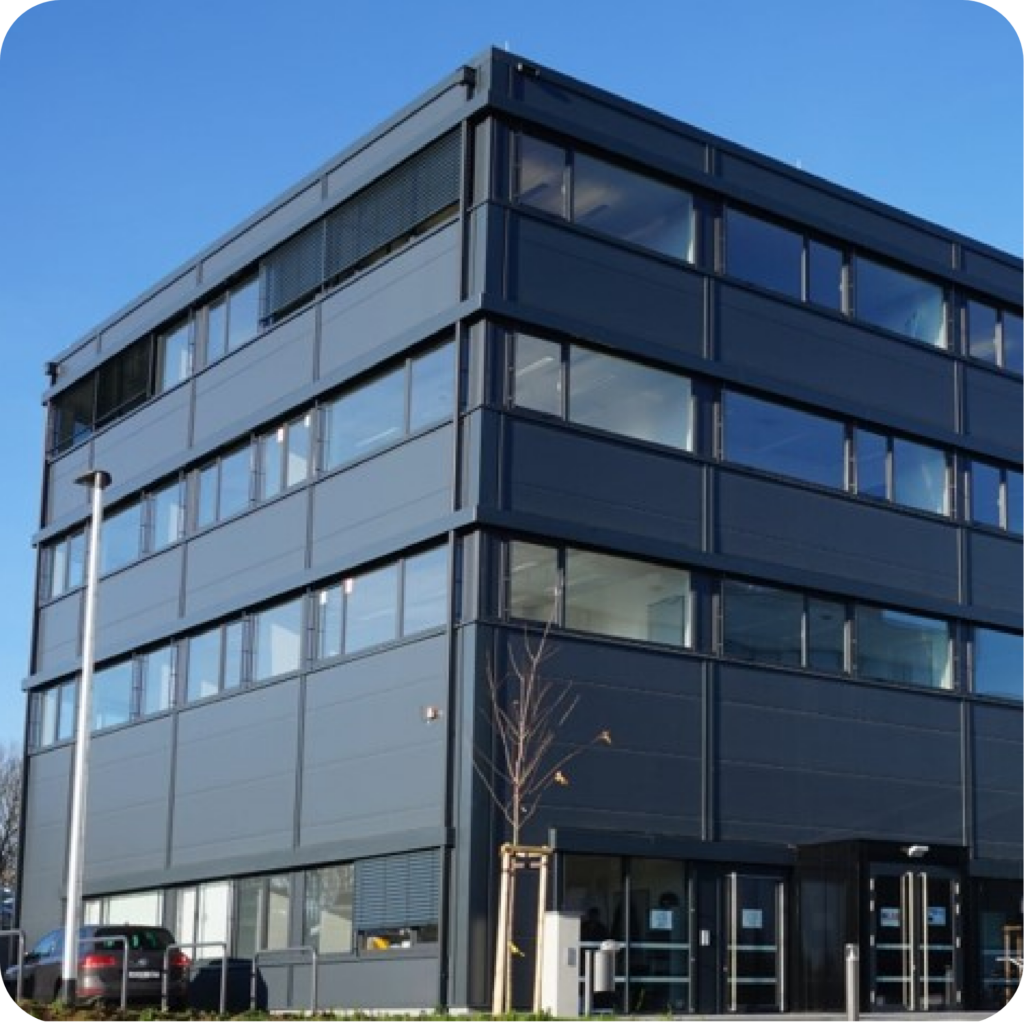
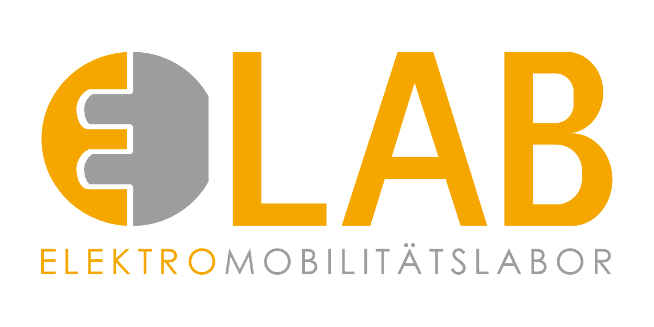
Has a total investment of €10 million and offers comprehensive testing solutions throughout the battery production process. Their facilities cover testing from assembly to cell validation, equipped with infrastructure for testing process innovations and individual test bench configurations. They conduct a range of tests, including quasi-static and dynamic intrusion tests, abuse tests with gas analysis, volume flow measurements, and thermal propagation testing.
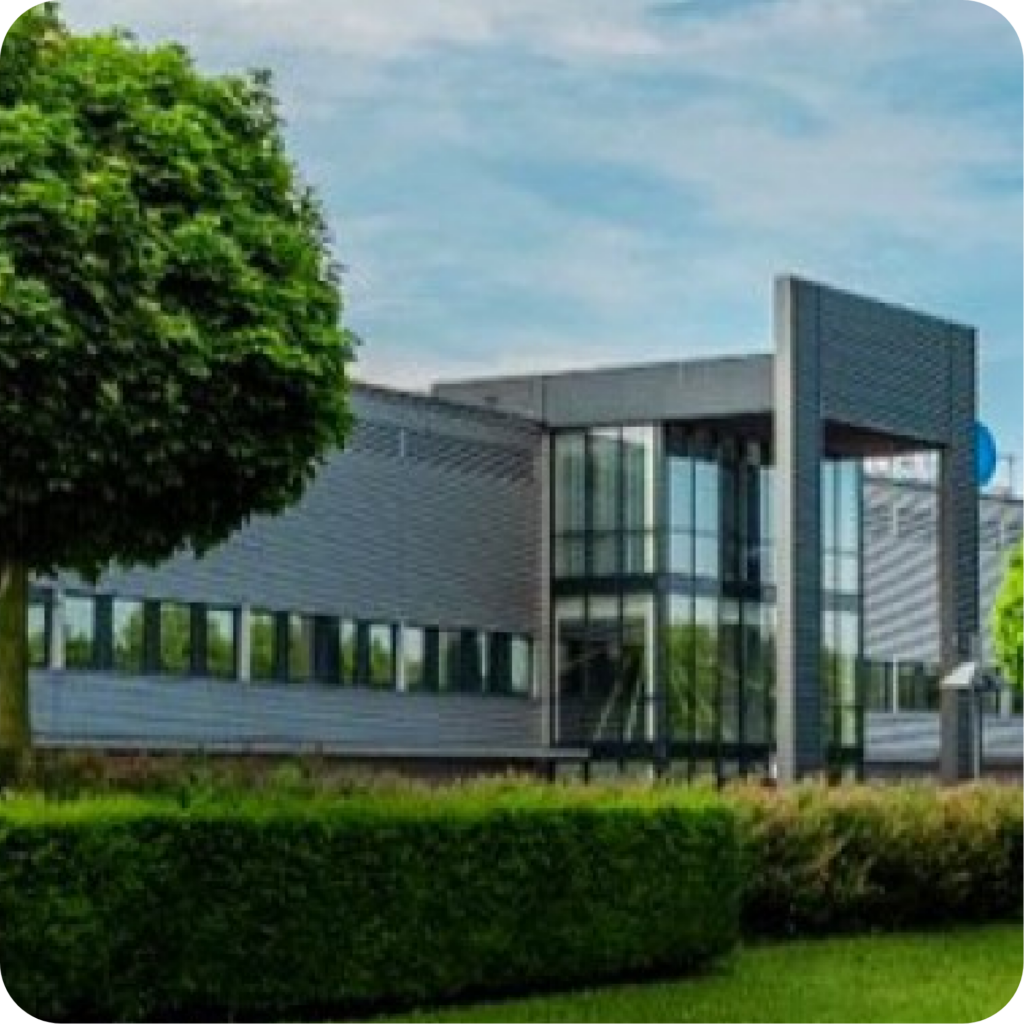
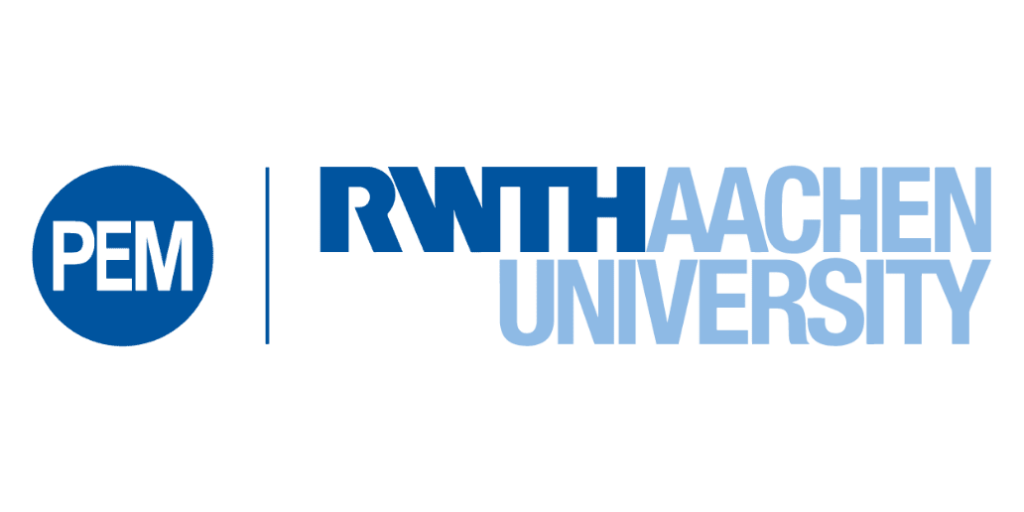
Specializes in battery engineering and safety. Their “Battery Engineering & Safety” group focuses on the development and safety of lithium-ion battery systems. They leverage simulations and reality tests to focus on the mechanical, electrical, and thermal design of battery cells, modules, and packs. Their research extends to novel battery system architectures and product innovations at all levels.
USE CASES
Welcome to our case studies section, where we showcase real-world examples of the projects we have completed. These case studies offer insight into the breadth and depth of our expertise in battery testing solutions. From concept to execution, each case study highlights the unique challenges we have faced and the innovative solutions we have offered our customers.
Empowering Safety in Li-ion Battery Storage for a TIER1 Automotive Supplier
In our quest to bolster safety standards for a leading TIER1 automotive supplier, we addressed the challenge of Thermal Propagation Prevention (TPP) Testing with precision. We meticulously designed experiments, adjusting TPP material parameters, and conducted rigorous propagation tests within certified environments. Our analysis yielded invaluable quantitative performance data, highlighting the effectiveness of different TPP material variants.
This thorough process identified optimal material configurations, promising to elevate battery storage safety standards significantly.
Addressing Thermal Propagation Prevention in Battery Development
In battery development, Thermal Propagation Prevention (TPP) is a critical concern. Despite its gravity in battery safety, a universally reproducible test standard for TPP materials remains elusive. Our systematic approach defined precise test stand requirements covering different cell formats, TPP materials, and scenarios. With a focus on reproducibility, we developed a highly precise test method aligned with these needs. Utilizing advanced CAD software, we meticulously constructed the TPP test stand, ensuring comprehensive detailing in the Bill of Materials (BOM).
The result? A triumph of methodical engineering: fully customizable CAD models and detailed BOMs, laying a solid foundation for standardized TPP testing in battery development.
Enhancing BoL Testing Efficiency for OEM Module Production
Tasked with optimizing the BoL testing for an OEM’s module production line, we employed a multifaceted approach. We identified key cell quality parameters crucial to the process and used various measurement technologies like EIS, CT, and Ultrasound to enhance efficiency. With precision and innovation, we designed a customized measurement station tailored to the production environment. Rigorous validation exercises refined cutting-edge technologies, ensuring seamless integration into production.
The outcome: A validated technology concept poised to revolutionize BoL testing, ensuring heightened productivity and quality assurance.
LET'S MEET!
Book a meeting for more detailed information